Opti-6G
Industry 4.0
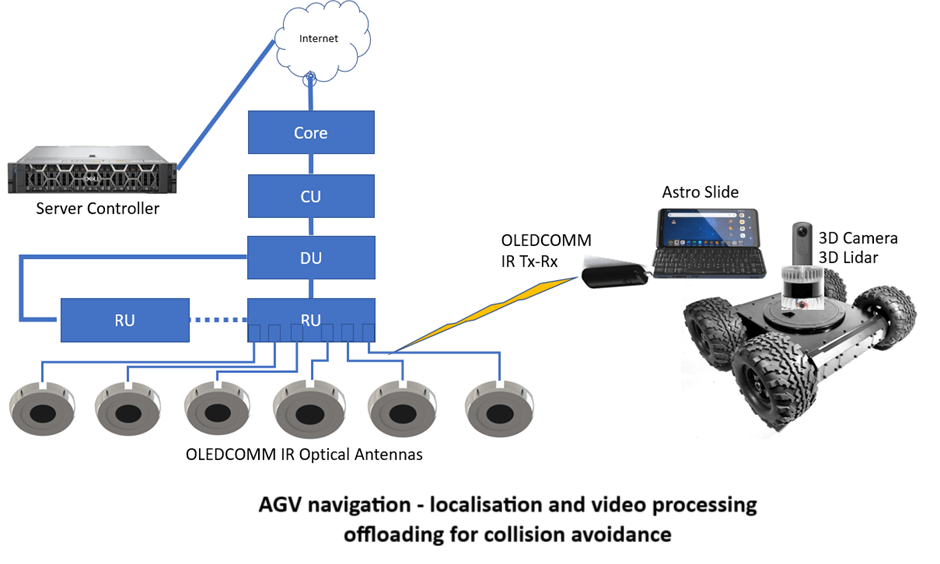
Smart transportation vehicles
In the factories of the future, AGVs will play an important role in the delivery of such tasks as driverless and autonomous transport of material and goods from and to production lines. They also can carry robot equipment (e.g., a robot or gripper arm) to flexibly support the assembly process. In this use case, we focus on two important features of AGVs:
- Video processing offloading from an AGV camera to the neighbour edge computing node with high requirements on data rate (>500 Mbps),
- Localisation of an AGV in different scenarios with high requirements on accuracy for the localisation (< 1 cm).
These functions require a wireless communication network for data transfer and localization purposes to be processed in a local or remote data centre. The localisation of an AGV using ToA and AoA from one or more 6G NB access points to identify position and an HD camera observing the AGV environment to avoid collision with moving objects is an example of a Mobile AGV application in industry.
An AGV fleet provides intra-logistic transportation and traversing in the factory. An AGV can also be part of an assembly process by picking and placing parts using a gripper arm with sensors mounted on the AGV. An example of the AGVs that have been built are the Lynxmotion - A4WD3 Rugged Wheeled Rover and the Pimoroni AGV robot Trilobot. Twenty of the latter are being built to create a swarm of AGVs for illustrating I4.0 use cases.
Wireless high-quality video cameras and co-located LIDARs are easily deployed on mobile platforms like AGVs. The video and point clouds from these cameras can be used to send high-quality and high frame rate video to an image analysing system located at the “factory edge”. By this, a new level of production monitoring is unleashed enabling a long list of new features such as accurate object detection and tracking around AGVs, anomaly detection on the shop floor, improved safety, process tracking and logging, etc.
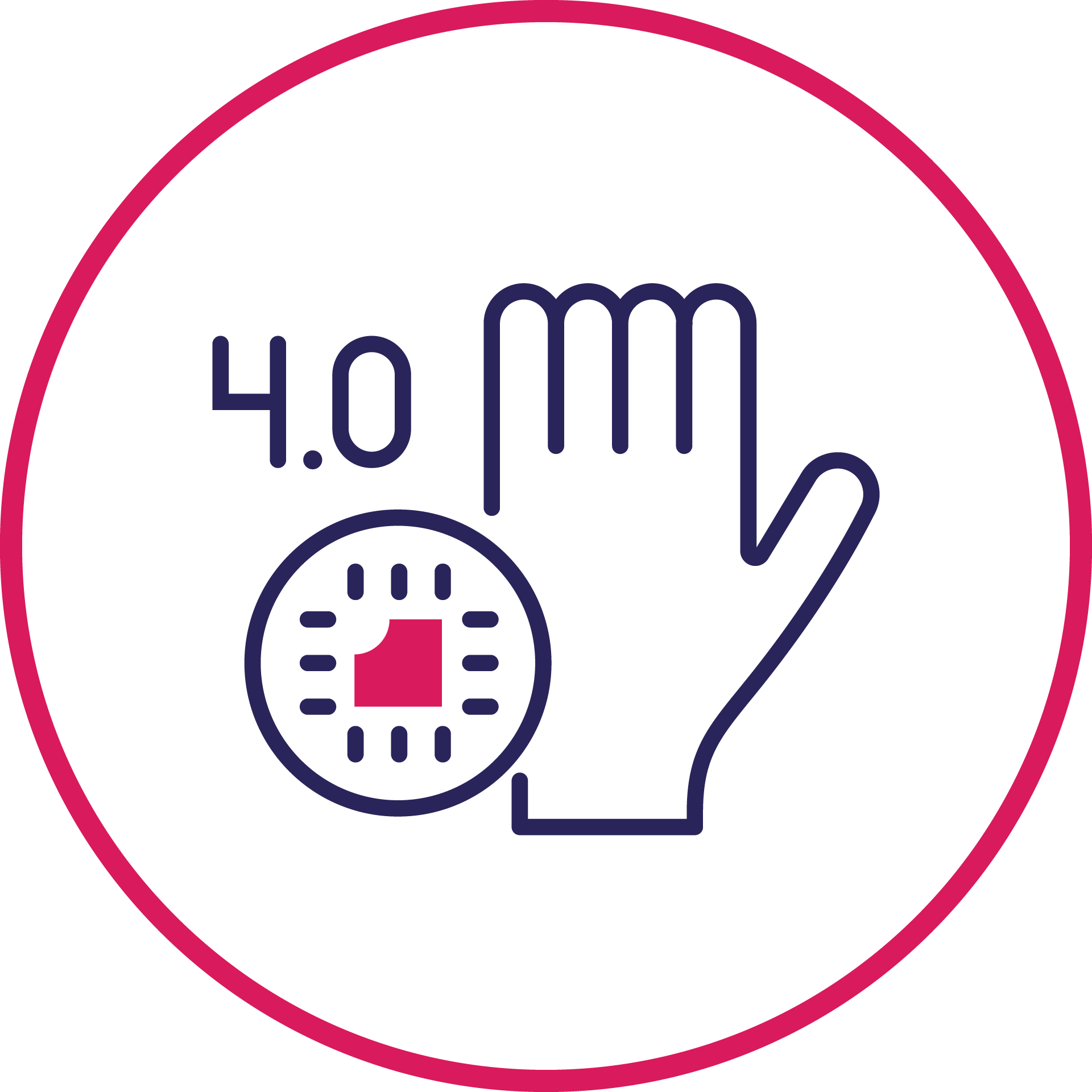
Opti-6G
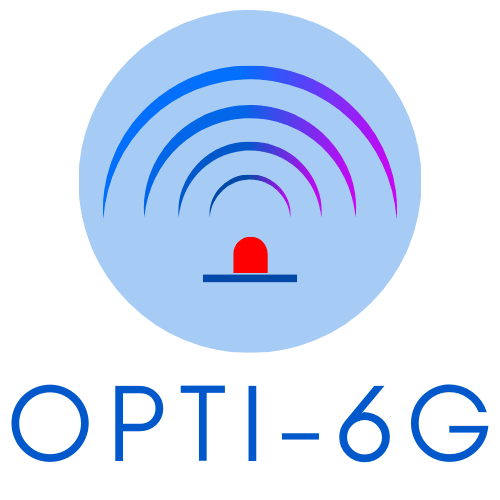